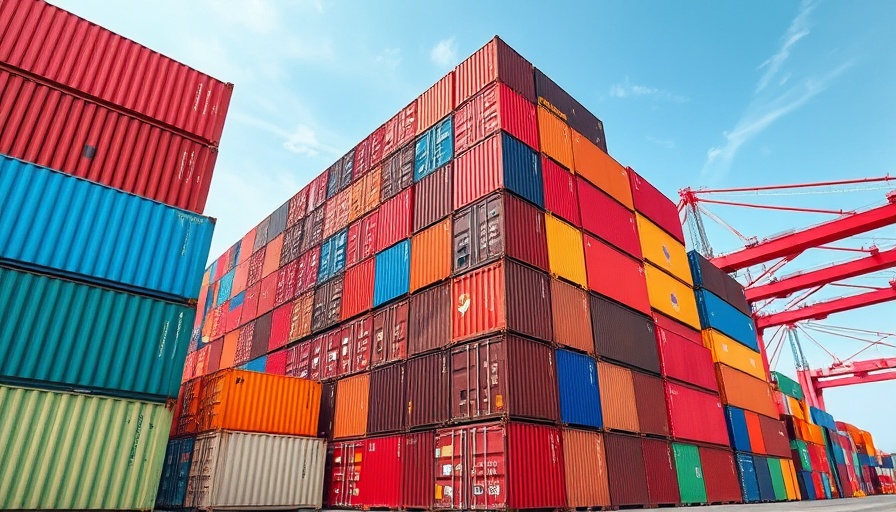
Understanding Supply Chain Vulnerabilities in Construction
The ongoing strikes at East Coast ports have drawn significant attention to the vulnerability of our construction supply chains. Delays in receiving vital materials not only stall projects but also inflate costs, a pressing concern in an industry already battling rising expenses related to labor and materials.
The Variety of Construction Materials at Risk
Construction materials imported through East Coast ports are particularly susceptible to delays during such strikes. A wide array of essential supplies from both established and emerging markets are affected. For instance:
Lumber and Engineered Wood Products: Plywood and oriented strand board (OSB) often come from Canada and South America, while exotic hardwoods are imported from Africa. Cross-laminated timber (CLT) from Europe is also crucial for modern construction, emphasizing the increasing reliance on foreign supplies.
Stone, Tile, and Flooring Materials: Italy and Brazil are significant suppliers of granite and porcelain tiles. Any delays in these imports can disrupt high-end projects that require specific aesthetics and materials.
Steel and Metal Products: Critical supplies include structural steel from Turkey and rebar from Ukraine, materials integral to building safety and durability.
Regional Differences in Construction Supply Chains
While East Coast ports handle a diversity of imports, West Coast ports typically dominate Asian trade. This geographical division has implications not only for the cost but also for the timing of material availability. As the Panama Canal expansion facilitates more East Coast entries from Asia, a shift could impact how quickly materials circulate in the market.
Strategies to Mitigate Delays
For contractors and project managers, understanding potential delays in material shipments presents both a challenge and an opportunity. It is essential to foster relationships with multiple suppliers to mitigate risks associated with single-source dependencies. Here are some strategies to consider:
- Diversifying Supply Sources: Expanding the network of suppliers beyond those reliant on a single port can help reduce the impact of regional disruptions.
- Stockpiling Key Materials: Maintaining an inventory of critical materials can act as a buffer during delays, allowing projects to continue without substantial interruptions.
- Investing in Technology: Leveraging technology for supply chain tracking can provide real-time updates on the status of materials, aiding in project planning and risk management.
Economic Implications of Material Delays
The economic fallout from delays in construction materials can ripple through the entire market, impacting everything from housing prices to employment in the construction sector. As project timelines stretch, the costs associated with delays can escalate, pressuring budgets and lead to disputes that require legal resolution.
With construction being a critical driver of the economy, addressing these vulnerabilities becomes increasingly urgent. Stakeholders must collaborate to innovate solutions that ensure material availability, enhance logistical efficiency, and anticipate future disruptions. As the balance between cost and timely delivery becomes more fragile, adaptability remains paramount for all involved in the industry.
Write A Comment