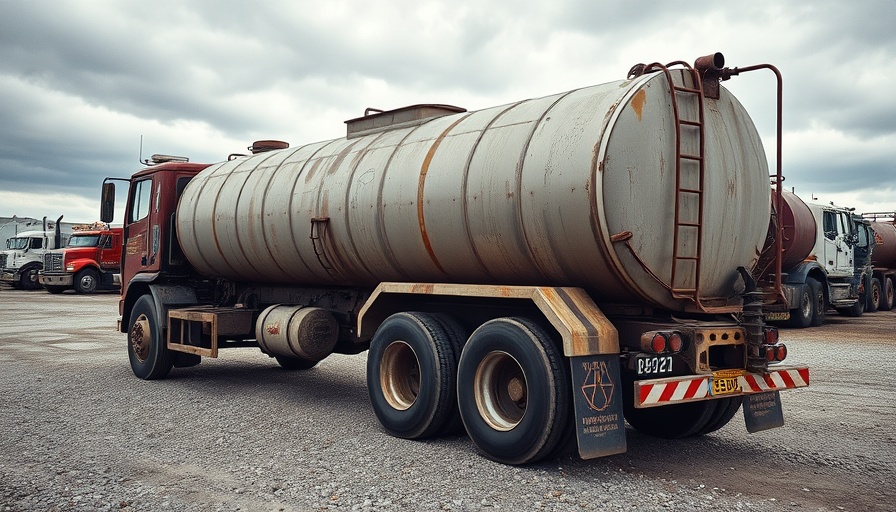
Understanding the Tragic Incident
On May 5, 2025, a tragic incident occurred involving a young wash bay attendant at a commercial trucking company in Kentucky. The 20-year-old, who had only been on the job for five months, lost his life due to an avoidable fire caused by a failure to adhere to safety protocols when dealing with compressed liquefied petroleum gas (LPG). This heart-wrenching event not only highlights the risks associated with handling hazardous materials but also raises questions about the safety measures in place for workers.
Key Lessons from the Incident
This case serves as a stark reminder of the importance of proper training and established protocols in the workplace. The tragedy unfolded when a maintenance employee incorrectly opted to open the trailer valve, allowing butane gas to escape through a hose onto the ground. When the wash bay attendant activated an electric grease gun underneath the tank trailer, the escaping gas ignited, engulfing him in flames.
Fortunately, another employee quickly intervened by pulling the attendant to safety and calling emergency services. However, despite being conscious during his transport to the hospital, he succumbed to his injuries seven days later due to multisystem organ failure caused by thermal injuries.
The Importance of Formal Procedures
Investigations revealed that the employer lacked a formal trailer flaring procedure and a dedicated training program for maintenance staff. The absence of these crucial elements not only placed employees at risk but also underlines the responsibility of employers to ensure workplace safety is prioritized.
To combat such tragic occurrences, businesses must:
- Establish and implement a robust trailer flaring procedure alongside comprehensive training for all staff involved.
- Utilize intrinsically safe tools around LPG trailers to prevent potential ignition sources.
- Create a structured health and safety program focused on preventing similar incidents.
- Clearly define and restrict employee duties to their designated scopes of work.
Fostering a Culture of Safety
It’s not just regulations that ensure workplace safety; it’s the culture of safety that an organization fosters. Workers need to feel empowered to speak up regarding safety concerns and report inadequate practices without fear of repercussions. Effective communication and constant emphasis on safety protocols can significantly reduce risks in hazardous environments.
The Future of Workplace Safety in the Industry
This heartbreaking incident is a call to action for businesses and industry stakeholders. As safety consultants and workplace wellness advocates, it's time to rethink the methodologies employed when managing hazardous materials. Incorporating new technologies and safety practices can lead to a safer work environment for both workers and employers while also improving overall productivity.
By committing to ongoing safety education, organizations can not only protect their most valuable assets—their employees—but also strengthen their reputation and efficiency in the long run.
Call to Action: Prioritize Safety in Your Business
In light of this tragic incident, we must urge all business owners and facility managers to take a proactive approach towards workplace safety. Implement necessary safety measures today to protect your employees and ensure a secure working environment. Consider conducting safety audits and provide training that encompasses safety protocols pertinent to your industry. The cost of neglecting safety is far greater than the investment in preventive measures.
Write A Comment